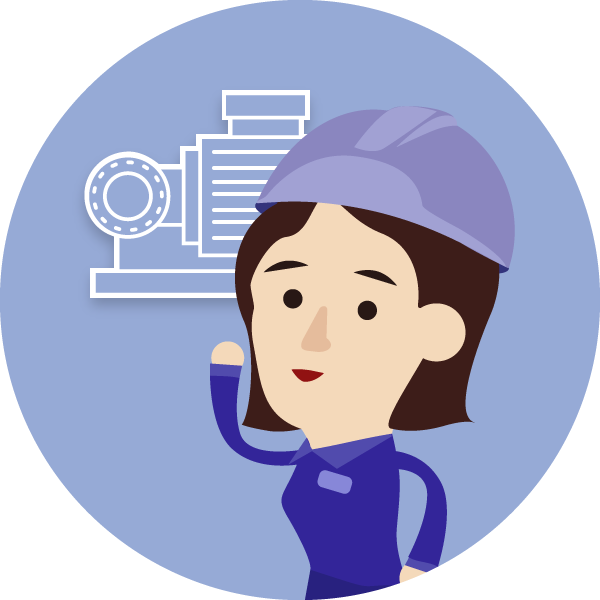
Pneumatic Valve Actuator Market Report To 2026
Prominent Market Research has produced a new report detailing the global pneumatic valve actuator market to 2026. Major industry players…
Purchasers often define the type of documents that vendors must supply as part of the supply contract. The Vendor Document Requirements (or VDR) is the list of those document types. Each line typically includes a document code, description, and delivery timeline (e.g. 10 days after order).
Perhaps you refer to the VDR as Supplier Document Requirements (SDR), Seller Data and Drawing Requirements (SDDR), Vendor Data and Document Requirements (VDDR), Supplier Document Requirement List (SDRL) or something else.
Whatever you call it, the VDR will additionally identify which codes should appear in document compilations like manufacturing record books, shipping dossiers and the like.
Once you’ve received the documents, you then need to actually build your document register.
Fortunately, DocBoss does this for you automatically.
We believe there is a very easy and consistent way to create vendor document registers. While DocBoss automates this process for our customers, it is a straightforward method you can use independently.
We start by identifying various “levels” in the order information. The biology keeners may remember taxonomy “ranks” like Kingdom, Class, Order, Genus, Species. When looking at order information, we start with the following levels:
Unit |
Tag |
Model |
Manufacturer |
Order |
Given a set of sample order data:
Line | Manufacturer | Model | Tag | Description |
1 | NewCo | XXX | 101 | Black Widget |
2 | NewCo | XXX | 102 | Black Widget |
3 | NewCo | XXY | 101 | Red Widget |
4 | NewCo | ZZZ | 101 | Container |
5 | Acme | AAA | 101 | Tool |
We can easily identify how many unique references are associated with each level .
Level | References | Qty |
Unit | [Line 1,2,3,4,5] | 5 |
Tag | [101, 102] | 2 |
Model | [XXX, YYY, ZZZ, AAA] | 4 |
Manufacturer | [NewCo, Acme] | 2 |
Order | [PO#1] | 1 |
The next step is the most critical component of the process to create document registers.
Lets assume the following document codes have been requested for the order
Code | Name |
A01 | MRB |
B01 | Quality Manual |
C01 | Safety Manual |
D01 | Drawing |
E01 | Material Test Report |
F01 | Completed Instrument Data Sheet |
Our realization is that each document can be associated to a specific rank. In most cases the below applies:
Code | Name | Level | Qty |
A01 | MRB | Order | 1 |
B01 | Quality Manual | Manufacturer | 2 |
C01 | Safety Manual | Manufacturer | 2 |
D01 | Drawing | Model | 4 |
E01 | Material Test Report | Unit | 5 |
F01 | Completed Instrument Data Sheet | Tag | 2 |
This gives you all POSSIBLE documents required on the order. A total of 16 documents.
Note that another step is often required, to determine which of these 16 documents are required.
If you’d prefer to do this work automatically and want to learn more about how DocBoss can help in this regard, contact us and let us know.
DocBoss is the only true document control system for
suppliers. Book a quick demo to see how we help process
equipment suppliers make more profit with less pain.