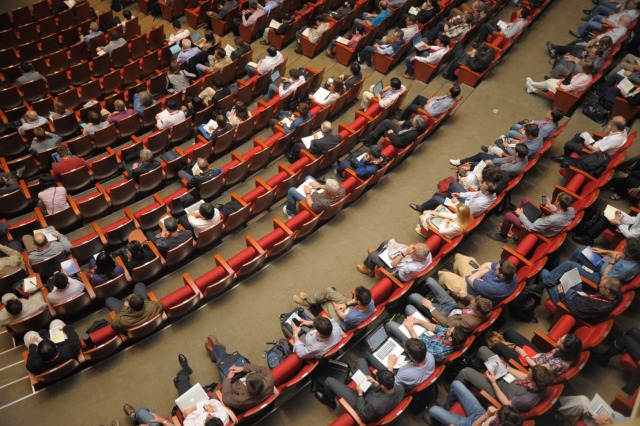
ASME Pressure Vessels Piping Conference (PVP)
The ASME Pressure Vessels & Piping Conference (PVP) takes place in Prague, Czech Republic from July 15-20, 2018. The exhibition…
We produced a detailed survey entitled Supplier vs EPC, Why is Vendor Documentation so Painful? that discusses the issues that suppliers of process equipment and the EPCs that they serve have with one another.
In addition to identifying the biggest pain points from suppliers, the survey process identified more general feedback which should be of interest to suppliers.
Various data points in the survey indicate that suppliers have fewer resources (and tools) available for document control:
• Fewer than 20% of suppliers reported having dedicated document control resources; The rest rely on project managers or technical resources to perform this work as required. We expect that the more technical a resource, the less time they can commit to document control.
• To manage data and documents, 75% of EPC respondents use an Electronic Document Management System (EDMS). However, only 2% of suppliers currently have an EDMS in place. Instead, they create and manage their documents using spreadsheets and pdf tools, leading to errors and rework.
• Almost all suppliers surveyed – a full 90% – reported using email regularly to send and track transmittals. By contrast, 49% of EPCs declared this to be their preference.
Using an EDMS allows detailed tracking for documents. Email for transmittal management has some significant drawbacks: searching to track down submissions; weak audit trails; and non-deterministic delivery (you don’t know if it was received). Interestingly, the majority of EPC respondents (68%) expressed a willingness to log into a vendor system to receive submissions.
The most experienced supplier document control experts seem to have access to an EDMS at their workplace. In fact, supplier document controllers with more than five years’ experience were three times as likely to be an EDMS user.
If you’re a supplier of process equipment, are you serving your EPC customers in a way that they are happy with?
DocBoss is the only true document control system for
suppliers. Book a quick demo to see how we help process
equipment suppliers make more profit with less pain.